Los materiales del futuro
Es más gratificante hacer realidad las ideas que soñarlas. Los desarrolladores de Porsche se dedican a convertir tecnológicamente en realidad lo aparentemente imposible.
Porsche 911 Carrera T
Emisiones de CO₂ (combinado): 215–193 g/km
Consumo combinado: 9,5–8,5 l/100 km
Clase de eficiencia: G
Porsche 911 GT2 RS
Emisiones de CO₂ (combinado): 269 g/km
Consumo combinado: 11,8 l/100 km
Clase de eficiencia: G
(Datos de 2018)
A primera vista, no se aprecia ninguna innovación en el pedazo de chapa de acero prensada que Philipp Kellner deposita sobre la mesa. Al parecer, su lugar es el umbral inferior del vehículo. En él se encajarán las bisagras de la puerta en la parte inferior y el cristal del parabrisas desde el lateral superior, explica el experto de Porsche que trabaja en el Departamento de Montaje y Desarrollo Preliminar de Weissach. Se trata del pilar A, la primera vertical importante de la carrocería si se mira desde la parte delantera del vehículo. Junto con los pilares B y C, conforma el habitáculo de pasajeros en la mayor parte de los automóviles, por lo que es fundamental para nuestra integridad física especialmente en los vehículos abiertos, como cabriolets o roadsters. En ellos, el pilar A garantiza un espacio de supervivencia en caso de vuelco. En este perfil de fina chapa de acero encaja a la perfección otro perfil de acero ultrarresistente. El poco llamativo trozo de metal es ya de por sí una obra de ingeniería de primer orden, ya que tiene un grosor variable, más fino en los extremos y más macizo en el medio.
Una columna vertebral invisible
Una pieza de plástico negro en forma de malla circunda el resistente metal y lo refuerza desde dentro. «Lo que aquí no se ve es que entre el metal y el plástico reforzado por introducción líquida de fibras cortas de vidrio hay dos placas más de tejido de fibra de vidrio termoplástico. Lo llamamos ‹organochapa›», explica Kellner. En conjunto, todo ello conforma el pilar A híbrido 3D, un novedoso método de construcción inventado por Porsche. Su gran ventaja es que, al igual que los pilares A actuales de los cabriolets hechos de tubos de acero ultrarresistente, no se dobla en caso de vuelco, siendo más de 5 kilogramos más ligero a igual rendimiento. «Las carrocerías de construcción ligera del futuro combinan diferentes materiales muy ligeros, como el acero ultrarresistente, el aluminio, el magnesio o el plástico reforzado con fibra de carbono. Pero, además, también entran en juego los nuevos métodos de construcción híbridos», explica Mathias Fröschle, Director del Departamento de Montaje y Desarrollo Preliminar. La protección de los pasajeros es capital en Porsche, y la construcción híbrida en 3D no solo respeta este principio, sino que además es más ligera y cuesta poco más que las soluciones que había hasta ahora.
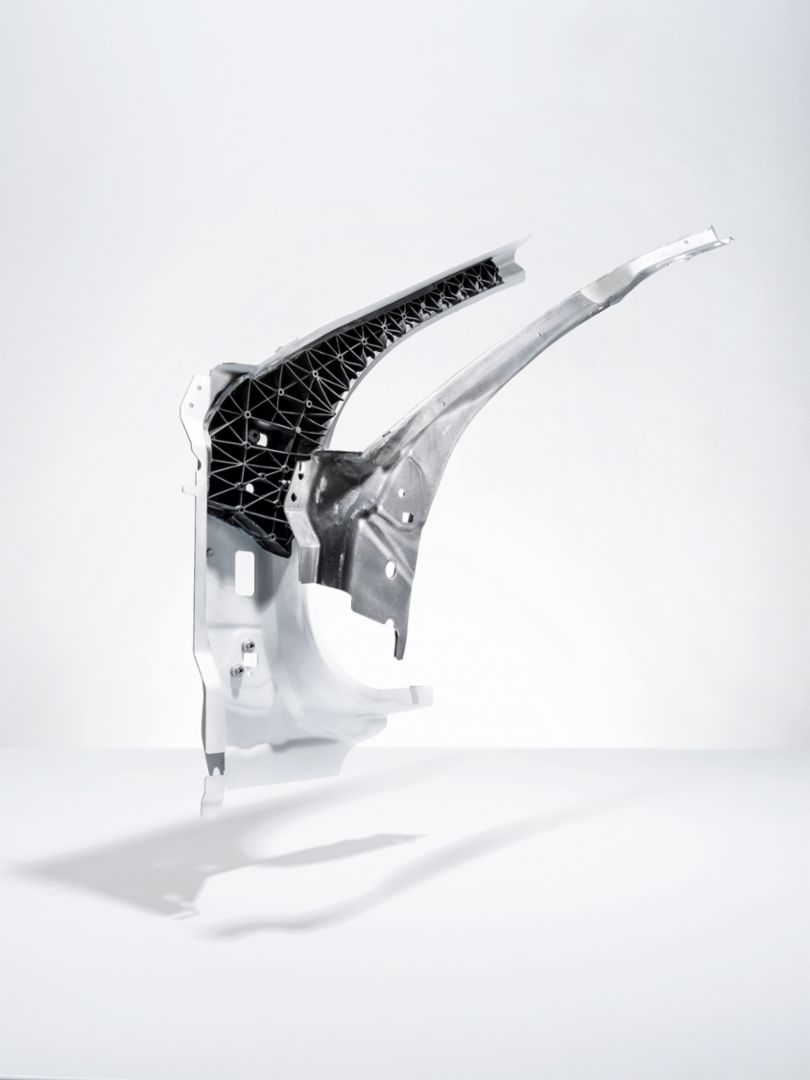
Pilar A híbrido 3D
En lugar del clásico tubo de acero de los pilares A, se trata de un inserto de acero ultrarresistente revestido de placas de tejido de fibra de vidrio termomoldeadas y circundado por plástico reforzado con fibras cortas de vidrio. El resultado es que, con un peso mucho menor, resiste igual de bien en caso de vuelco. Gracias a una estructura de soporte optimizada con nervadura de plástico, la pieza no se dobla sino que cede elásticamente. La investigación de esta novedosa tecnología se cerrará con éxito este mismo año, lo que permitirá su aplicación en las carrocerías de construcción ligera de Porsche.
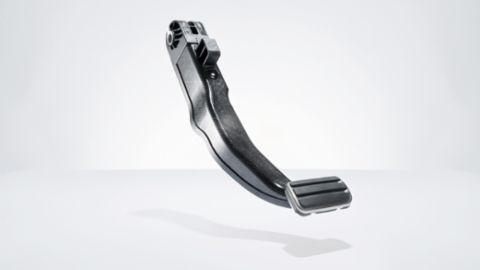
Pedal de freno
Ya a día de hoy, los conductores del actual Panamera y del 918 Spyder encuentran en la zona de los pedales de su deportivo un material que en el futuro podría ir dentro de los pilares A, ya que el pedal del freno está hecho exactamente de ese mismo material termoplástico compuesto.
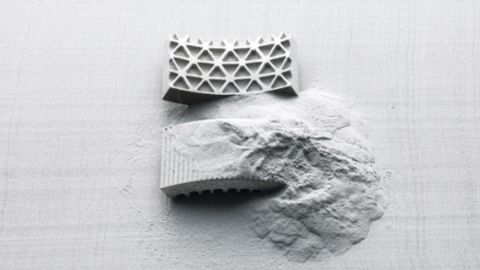
Polvo ultrafino de acero inoxidable
Hasta ahora, las formas complejas eran coto exclusivo de la fundición. Pero los denominados métodos de fabricación aditiva están revolucionando el sector. En este caso un láser va fundiendo el polvo capa por capa hasta lograr casi cualquier forma deseada.
Los conductores de los 918 Spyder y del Panamera actual pueden ver el punto de partida de esta investigación en el pedal del freno, donde brillan unas fibras negras. La mayoría da por hecho que se trata de fibra de carbono, pero Edgar Grundke, de Desarrollo de Pedales y Accionadores de Porsche, niega con la cabeza: «Son placas de fibra de vidrio termoformadas con una estructura de plástico reforzado con fibra de vidrio detrás». Es decir, exactamente lo mismo que en el futuro podría dotar de resistencia a los pilares A. «Es un material homogéneo, pesa menos que el metal y presenta una estabilidad duradera», explica Grundke. «Ningún otro fabricante se había atrevido a usarlo en la producción en serie. Nosotros somos los primeros». En el futuro el nuevo pedal de freno se implementará en otros modelos. Todo un motivo de orgullo. La audacia de Porsche ha merecido la pena. Lo confirma también Hendrik Sebastian, de Gestión de la Innovación y Desarrollo Preliminar de Weissach. Aquí es donde confluyen todos los resultados de las secciones de Desarrollo Preliminar, pero también se desarrollan ideas para el futuro, se valoran y ponen en marcha investigaciones y se observan tendencias. Las preguntas que se plantean aquí son como mirar en una bola de cristal: ¿qué querrán los clientes dentro de 5, 10 ó 15 años?, ¿qué tecnologías estarán disponibles? Además de capacidad de abstracción e imaginación, es necesaria una gran dosis de perseverancia en el camino hacia la implementación. Los responsables de desarrollo de Porsche tienen una máxima muy clara: «Excelencia en el rendimiento en todas las situaciones de conducción. Con nuestros deportivos nos movemos siempre al límite de lo técnicamente viable. Los nuevos conceptos de materiales y de producción son aquí imprescindibles, ya que solo así podemos garantizar un valor añadido sostenible para nuestros clientes», describe Sebastian uno de los objetivos del departamento.
«Con nuestros deportivos nos movemos siempre al límite de lo técnicamente viable. Para ello, son imprescindibles los nuevos conceptos de materiales y de producción». Hendrik Sebastian
Para seleccionar los materiales y posibles métodos de producción, los expertos de desarrollo reciben el apoyo del Departamento de Técnica de Materiales bajo la dirección de Stephan Schmitt. En este campo hay que tener amplitud de miras. Un ejemplo: la mayoría de smartphones se fabrican con Gorilla Glass, una fina lámina de cristal de alta resistencia con unas propiedades ópticas perfectas. «En el 918 Spyder con paquete Weissach montamos por primera vez un material muy similar, es decir, un cristal de material compuesto formado por dos capas de cristal fino con una lámina entre ellos», explica Markus Schulzki, de Montaje y Desarrollo Preliminar, mientras muestra un trozo de cristal de unos 20 cm². Se trata de la luneta situada entre los arcos tras los asientos del 918 deportivo. Es de una ligereza sorprendente. Cuando la tocas, suena a plástico. «Eso es lo que todo el mundo cree», revela Schulzki, «pero es cristal. Esto solo fue una prueba, ahora estamos mucho más avanzados». En el actual 911 GT2 RS y 911 Carrera T, las ventanillas laterales traseras y la luneta trasera están hechas íntegramente de cristal fino, ya que por iniciativa de Porsche ahora hay a disposición cristales curvos. Hasta hace poco, no era técnicamente posible. El grosor del cristal no llega a los dos milímetros, pesa aproximadamente un 40% menos y es la mitad de sensible a las picadas de piedras. Además, ofrece una protección casi del 100% frente a los rayos ultravioleta, un aislamiento térmico mucho mejor y una mejor insonorización. «Se filtran las altas frecuencias causadas por el flujo del aire en la marcha, pero no las frecuencias bajas. Así, el maravilloso sonido de, por ejemplo, un bóxer de seis cilindros se escucha con mayor nitidez». Schulzki no oculta su pasión por los motores clásicos.
Una revolución de cristal en la cabina
Con el smartphone, la tecnología de la comunicación ha puesto a disposición del sector del automóvil un material que también puede emplearse como transmisor de información en el vehículo. En el departamento de Mathias Fröschle, además de componentes externos también diseñan soluciones para el interior. Su visión: «Una consola central íntegramente de cristal fino con una superficie curvada. Las láminas permiten crear pantallas y mandos a la medida del conductor y el copiloto. El menú se activa por gestos y una respuesta táctil a través de contactos en el cristal confirma que la orden se ha ejecutado».
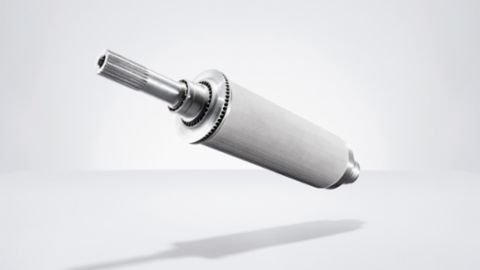
Eje rotor
Con los métodos de fabricación tradicionales, el núcleo de los motores eléctricos tenía que producirse a partir de varios componentes. La fusión por láser permite una fina nervadura en el interior empleando mucha menos cantidad de material. De esta manera, el eje es significantemente más ligero.
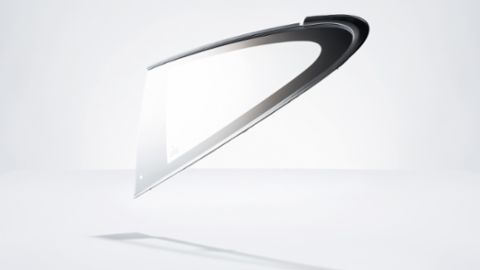
Ventanilla lateral del 911 GT2 RS
La ventanilla lateral ultrarresistente del 911 GT2 RS, curvada en todas las dimensiones, no solo mejora la relación potencia/peso, sino que también filtra y silencia el ruido del viento, a parte de ser un 40% más ligera. En la imagen, un prototipo.
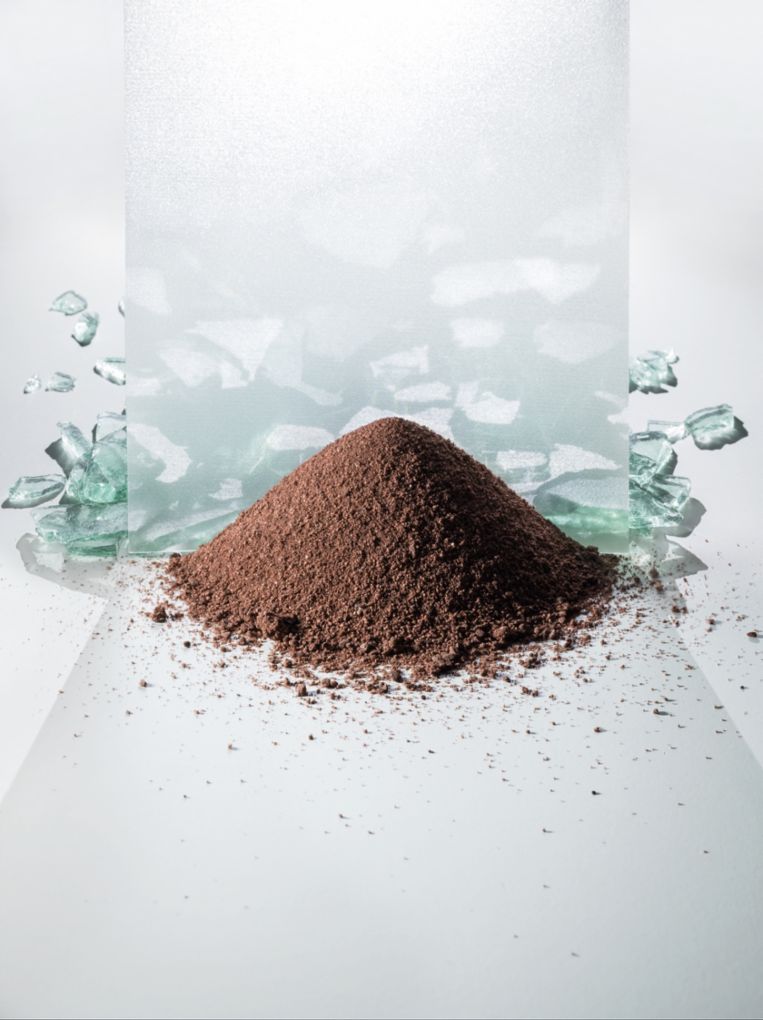
Cristal Gorilla Glass
La idea de un cristal fino ultrarresistente proviene de las pantallas de los teléfonos móviles y los ordenadores portátiles. Porsche es el primer fabricante automovilístico que utiliza de forma consecuente este vidrio laminado que lleva arena, cristal reciclado y una película de seguridad. Cada vez se usa en más modelos, pues el cristal fino es más estable y ligero, ofrece una mejor protección frente a los rayos ultravioleta y en el futuro incluso podría ofrecer funcionalidades de pantalla.
Hendrik Sebastian y sus compañeros creen que también son posibles otras aplicaciones: «Formas completamente nuevas, cristales y pantallas de realidad aumentada. Los pasajeros ven un castillo por la ventanilla y tocan la superficie de cristal. Una cámara lateral lo enfoca, coteja la imagen con información de Internet y la muestra en tiempo real junto al castillo en la misma ventanilla». La lámina entre las capas de vidrio funciona como una pantalla. No es ninguna ilusión óptica, es tecnología que ya está investigándose. También es posible un oscurecimiento de adaptación continua en función de la intensidad del sol o las preferencias de los pasajeros.
Deportivos de fibras vegetales
Paralelamente, Porsche también está estudiando materiales renovables para elementos de la cabina. «Ya existen revestimientos de puertas de fibras vegetales, pero aún no cumplen los requisitos que tiene que exigir un fabricante premium como nosotros», resume Fröschle. No obstante, Porsche pronto dispondrá de componentes convincentes en todos los ámbitos. «En 2048, no habrá ningún Porsche fabricado íntegramente con algas o fibras vegetales, pero la sostenibilidad y el reciclaje son temas que cada vez serán más relevantes», asegura Sebastian convencido. «Lo importante es que, aparte de materiales innovadores tengamos en cuenta nuevos métodos de producción, como la fabricación aditiva».
Se refiere a lo que comúnmente conocemos como impresión en 3D, y es la especialidad de Falk Heilfort y Frank Ickinger, de Desarrollo Preliminar de Motores, que muestran un cuerpo cilíndrico. Se trata del eje rotor de un motor eléctrico que traslada el par generado electromagnéticamente al engranaje, el cigüeñal de un motor eléctrico por así decir. «Este eje rotor está fabricado con un acero inoxidable especial», explica Heilfort. Junto al eje hay un pequeño tubo de cristal con un polvo gris muy fino, que es la microscópica materia prima de la pieza compacta. En una sala estéril, este polvo se distribuye finamente sobre una superficie y se fusiona con un láser de alta precisión para compactarlo. A continuación se esparce por encima otra capa de polvo y se vuelve a fundir. Capa por capa. De esta forma, a partir del polvo «surge» un eje rotor de unos 50 centímetros de largo. La ventaja respecto a una pieza fresada y rotada de forma convencional es que se requiere mucho menos material, el polvo sobrante puede reutilizarse inmediatamente y se pueden crear formas más complejas. El eje rotor lleva una fina nervadura en el interior que proporciona una mayor estabilidad.
En un torno, estas formas no se pueden lograr. Para obtener el mismo resultado, primero tendría que fundirse y luego soldarse una parte del eje. «Esto es una pieza, mucho más estable y ligera a la vez que con una rigidez superior y una adherencia mucho mejor», afirma Ickinger. De momento, la única desventaja es que «aún tardamos alrededor de 13 horas en imprimirlo». Por ello todavía no se planea su producción en serie, y sin embargo esta tecnología revolucionará la propulsión. Sebastian añade: «La fabricación aditiva está revolucionando el modo en que desarrollamos los componentes. Nos permite optimizar y probar las cosas mucho más rápido y además mejora considerablemente el rendimiento. Es una formidable innovación de producto y procesos con muchísimo potencial aún por exprimir. Quedan muchos desafíos todavía por delante, pero si nos echáramos atrás no seríamos Porsche». Un ejemplo de innovación en producto y proceso son los finísimos tubos de refrigeración curvados en mitad de una pieza. «Lo que estamos investigando aquí pronto nos llevará a grupos motor aún más compactos y con mejor rendimiento», asegura convencido Heilfort.
Ni renovables ni imprimidos en 3D. En el año 2048, los Porsche constarán de muchos materiales homogéneos diseñados de acuerdo a su uso específico. El acero y el aluminio se irán complementando cada vez más y mejor con materiales que permitan lograr una mejora en todas las dimensiones. Solo hace falta visión de futuro, ganas de investigar y valentía para innovar. Y a los expertos de Weissach no les falta nada de todo esto.